Blogs
Custom Injection Moulding
What is Custom Injection Moulding?
Custom injection moulding is the process of creating custom plastic parts by injecting molten plastic material at a high pressure into a metal mold. This process can be compared to making jello: to achieve the final product, you must fill the mold and then cool it to harden the surface.
This procedure was invented in 1872 by John Wesley Hyatt, an American inventor, when he needed an alternative product to fill up billiard balls instead of using elephant ivory which came from the tusks of elephants, in order to protect their at-risk population.
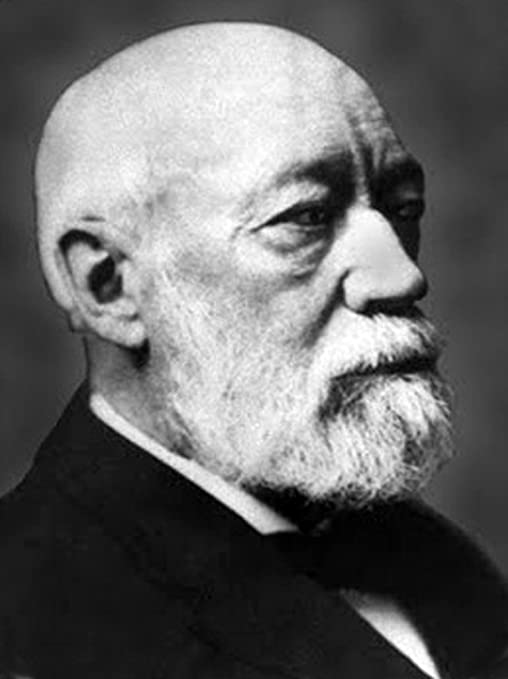
How does Custom Injection Moulding work?
The procedure used by machines for custom injection moulding can be broken down into three steps: injection, moulding, and clamping. Once the molten plastic is injected into the mold, the mold is cooled and opened to reveal a solid plastic part.
In order to increase flexibility for engineers and designers, there are many types of plastic resins and/or additives that can be used in the injection molding process, allowing them to go into more detail for moulding purposes.
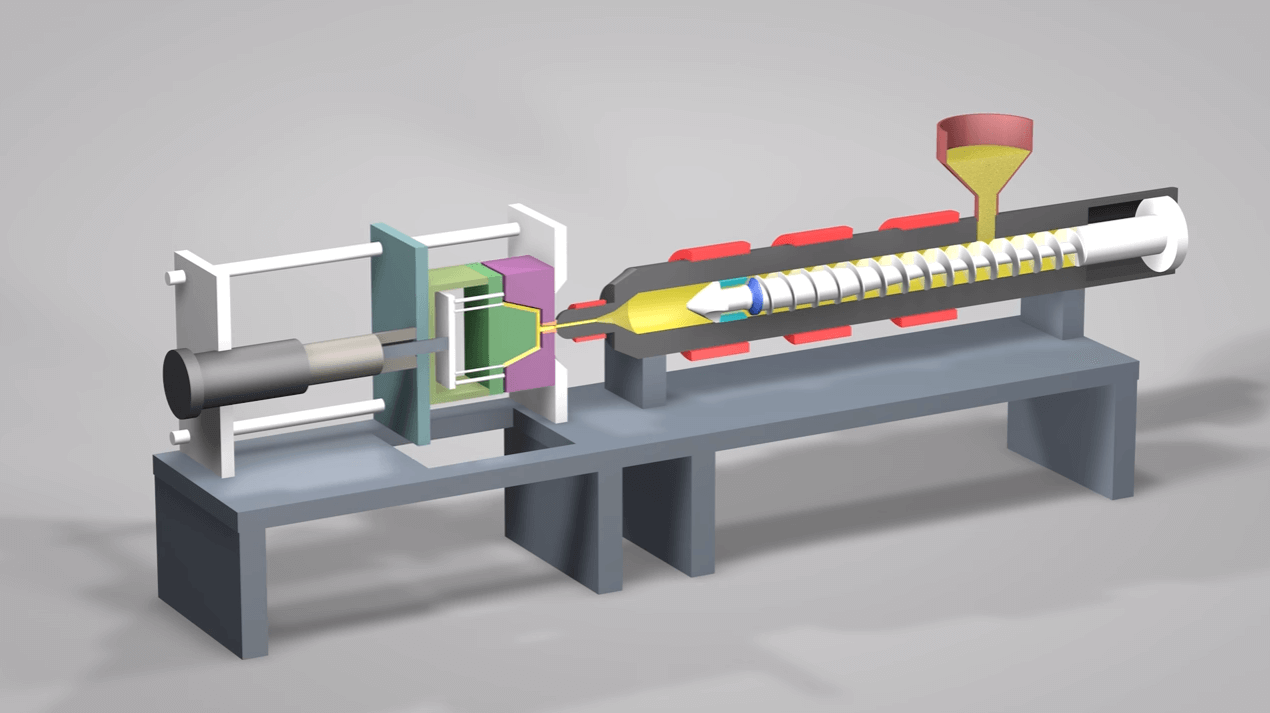
Benefits of Custom Injection Moulding
Custom injection moulding is beneficial for companies that want to create large or small custom parts at a high volume. Although injection moulds are typically made from steel or aluminum and are very expensive, the product cost per part can be economical if you need several thousand parts per year.
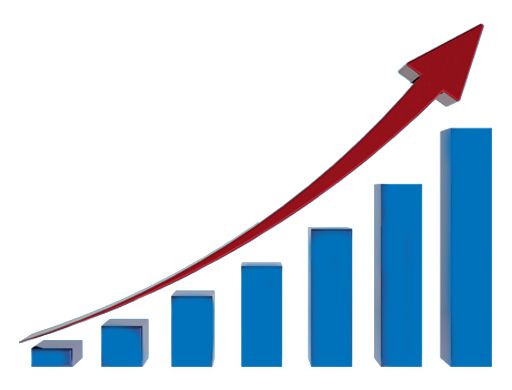
Examples of Products made from Custom Injection Moulding
Custom injection moulding can be used to create an infinite variety of plastic products, including:
- Surgical parts
- Car parts
- Chairs
- Toys
- Cutlery
- Lego bricks
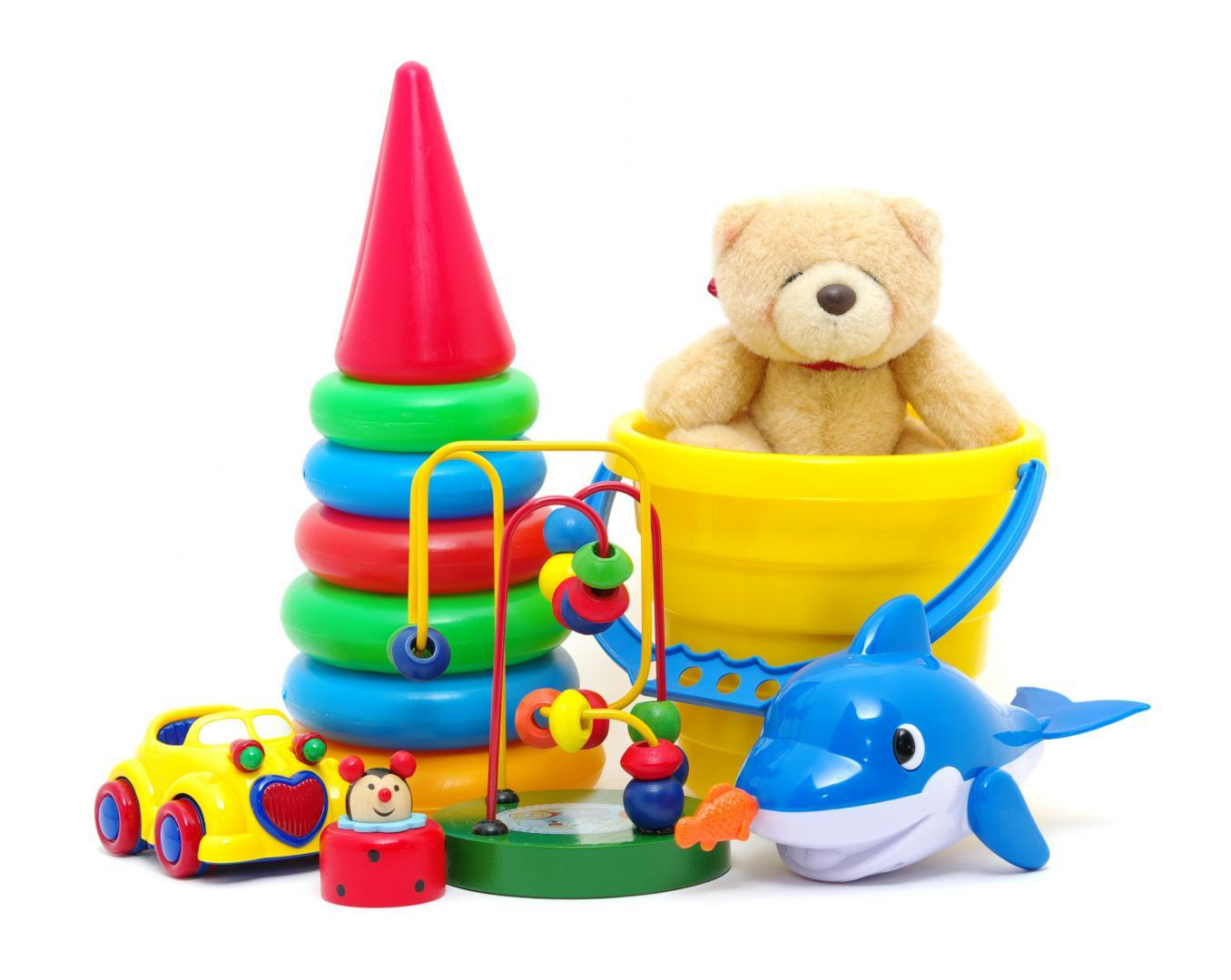
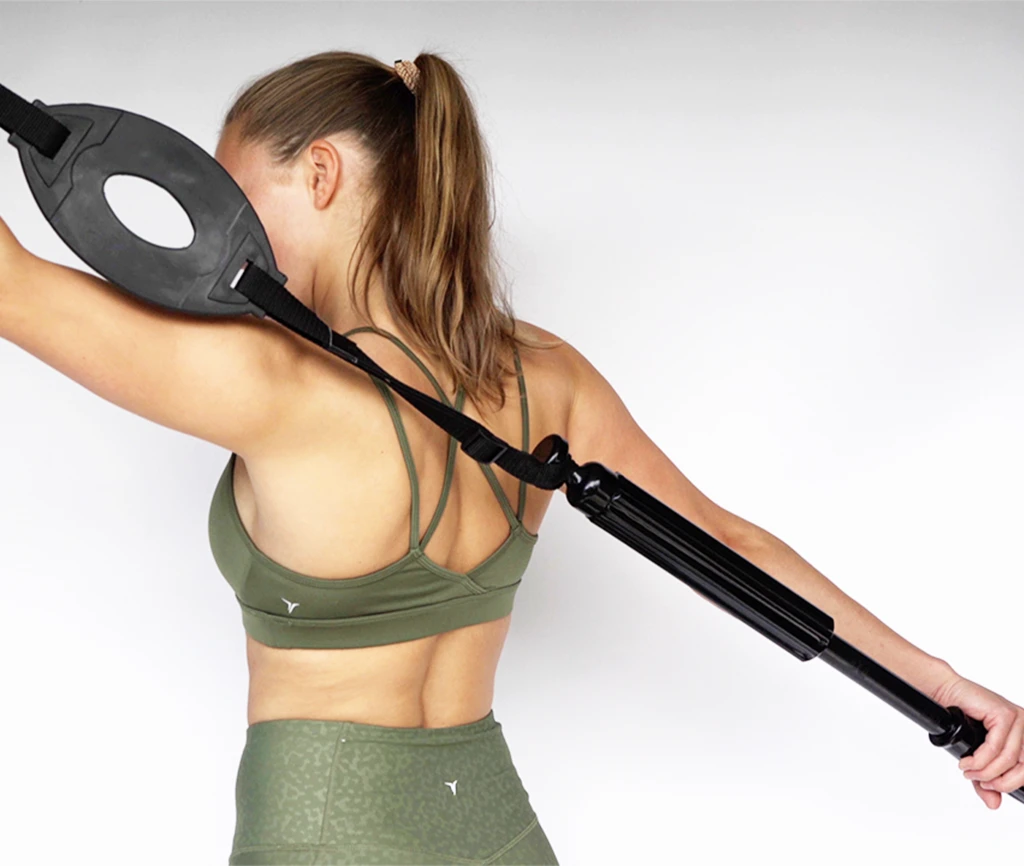
How can I Learn more about Custom Injection Moulding?
To learn more about custom injection moulding and its endless possibilities in the world of plastic manufacturing, feel free to reach out to a team member at Plasti-World for a free consultation.
Why you should use a North American company for plastic injection moulding
Plastic Injection Moulding and its Suppliers
Injection moulding is the manufacturing process in which plastic parts are produced by injecting molten material into a mould. Until recently, China has been the epicenter of plastic injection moulding services to the entire world.
However, due to the onset of the global pandemic, China has experienced a sharp decline in sales due to shut downs related to COVID-19. This phenomenon resulted in delayed lead times, which had a detrimental impact on customer deliveries.
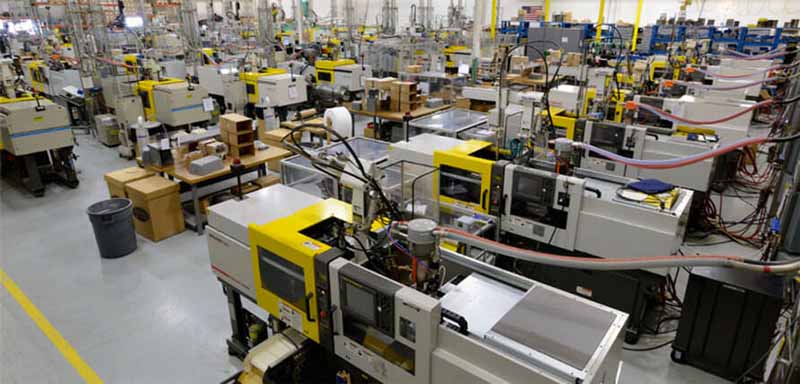
As a result of decreased production efficiency in China, consumers are looking elsewhere in order to diversify their supply chain, and to avoid the risk of being caught empty-handed in the next global pandemic.
Hence, this article explores why you should consider a North American manufacturing company for your plastic injection moulding services.
1. Product Quality
Chinese plastic production companies are known for their unbeatable product prices, primarily because of their remarkably low labor costs, overhead costs, and lack of foreign tariff impositions. However, in exchange for low prices, there is often a compromise on product quality.
This is primarily because certain companies do not prioritise hiring skilled labor to perform manufacturing duties. In addition, they don’t invest in high quality machines and hiring quality assurance managers.

In contrast, North American companies invest more time and money on product quality. For instance, they’re more willing to pay for a skilled workforce and high quality machines to perform plastic injection moulding.
2. Shortened Lead Times
When placing an order with Chinese manufacturing companies, consumers need to follow a strict timeline in order to receive their delivery on time. To elaborate, in order to ship products from Asia, clients would need to place their orders a minimum of 2 months (30 days production + 30 days shipping) in advance to account for potential shipping delays.
On the other hand, if a local client wanted to place an order for plastic injection moulding with a North American company, they would only need to do this 2 weeks in advance, due to geographical proximity and the reduced likelihood of shipping complications.
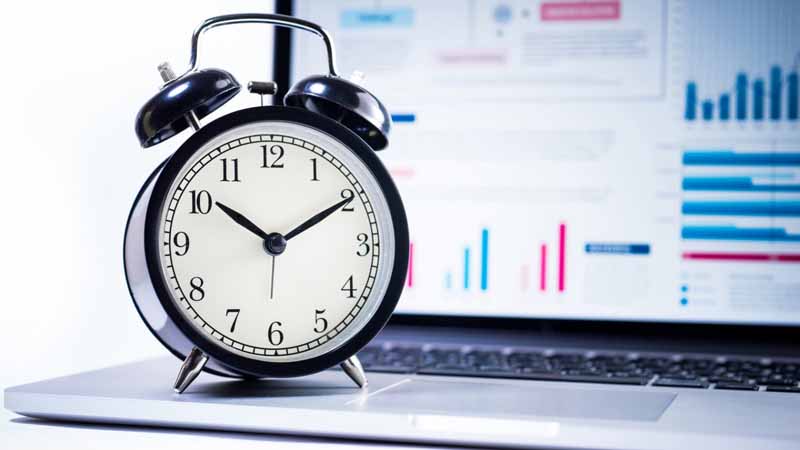
3. Payment Convenience
The vast majority of overseas and Chinese plastic manufacturing companies require clients to pay 100% of their order a minimum of 90 days in advance, before they receive their delivery and have the chance to monitor product quality.
In comparison, most North American companies only require their clients to pay for 100% of their order 30 days after delivery. With this payment method, clients have the opportunity to monitor the quality of the product, and reach out to the customer service facilities in the case that they’re unhappy with their order.
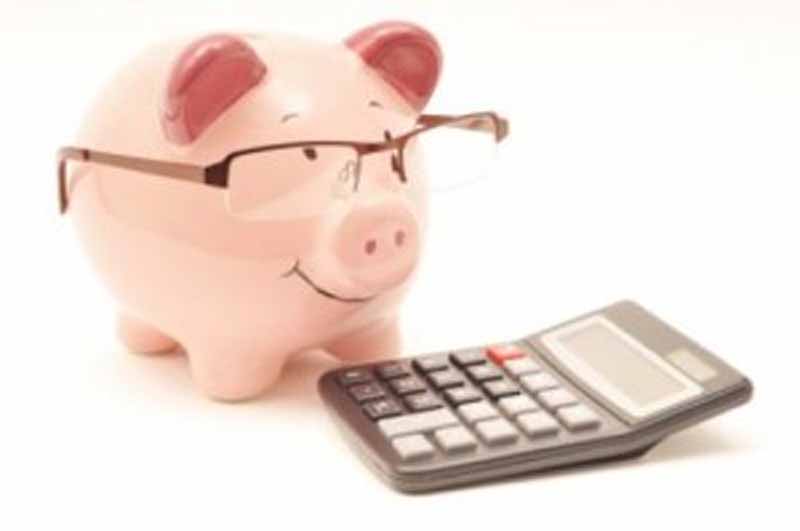
Concluding Remarks
In our rapidly changing world, there is a constant flow of unexpected events that impact the world’s economy and your decision to choose the right supplier for plastic injection moulding. Hence, it is wise to diversify your supply chain in order to avoid future delays caused by potential shutdowns or other phenomenons.
For these reasons, it would be tactful to consider obtaining supplies from a local North American plastic manufacturer, due to enhanced product quality, shortened lead times, and payment convenience.
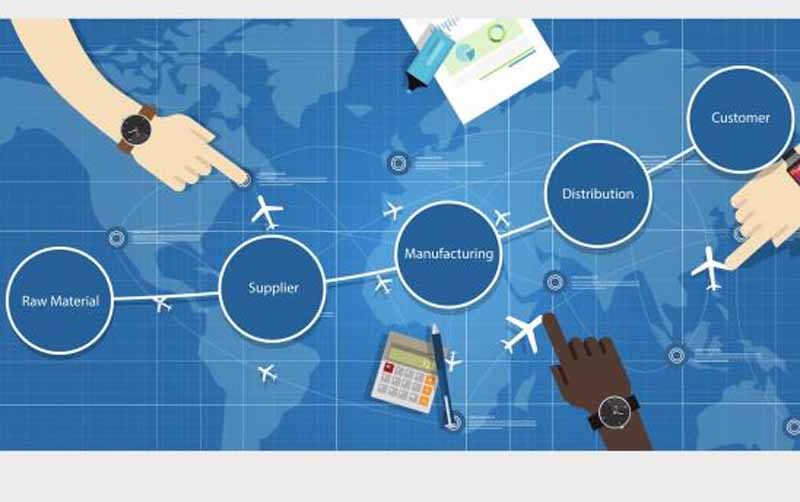
If you would like to get in touch with a local plastic manufacturer for your injection moulding services, feel free to reach out to a member of the Plasti-World team.